Снаряжение для выживания: Обработка металла. Часть 4.
О литье металла. Часть 1 — Печи для плавки.
Для начала приведу технологию плавления чугуна и стали в «высоких» печах которыми пользовались наши предки повсеместно по всему миру.
При сооружении высоких печей сначала выкапывали яму под горн. Насколько большими были такие ямы, сказать сложно, поскольку эрозия почвы и деятельность людей привели к разрушению их верхнего края. Судя по тем горнам, у которых сохранились обожженные края, некоторые ямы имели диаметр около 1,4 м и глубину примерно 75 см. Дно и стенки горна были иногда обработаны; в некоторых случаях обработка состояла в выравнивании их глиняной поверхности.
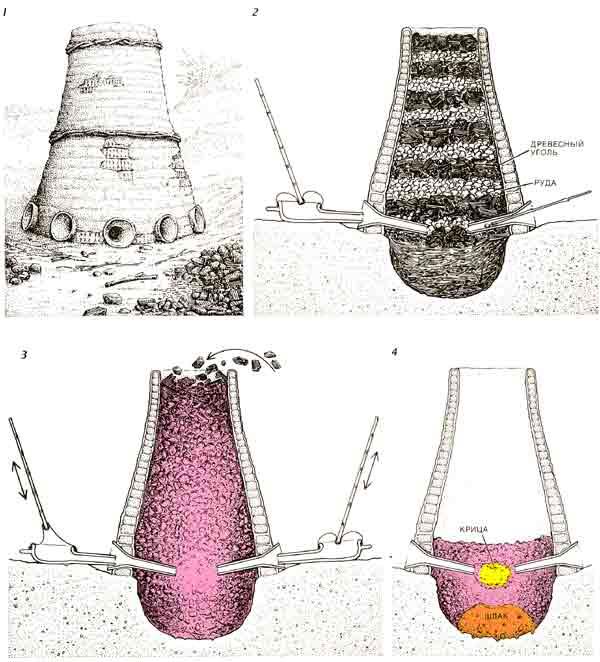
Шахта печи была оштукатурена и скреплена виноградными лозами для придания прочности (7). В основании печи располагались фурмы (трубы для дутья). Шахта загружалась чередующимися слоями древесного угля и руды (2). В открытый конец фурм вставлялись меха, огонь разжигали тлеющим углем, а дополнительное количество древесного угля загружалось сверху (3). Конечным продуктом была крица (4).
ОСНОВНЫМИ элементами, позволявшими использовать дутье, были фурмы. Эти глиняные трубки известны по этнографическим описаниям, а также по археологическим раскопкам. Судя по этнографическим описаниям, все фурмы изготавливали одним способом. Тщательно приготовленную влажную глину налепливали на круглые шесты; после того как глина слегка высыхала, шесты вытягивали, и таким образом получались глиняные трубки. Эти трубки, иногда вставленные одна в другую, вводили в основание печи. Внешнему концу некоторых трубок придавали воронковидную форму, с тем чтобы облегчить вдувание воздуха. Воронковидный конец трубки был обнаружен в стене печи, раскопанной в Гисагаре. Эта находка подтвердила предположение о том, что в печах железного века использовалось дутье.
Вполне вероятно, что в открытый конец фурмы вставляли меха. До сих пор археологами не найдены меха, однако о них часто упоминается в этнографических описаниях, относящихся к Межозерью. Меха, используемые в этом районе и в настоящее время, состоят из крупного сосуда, изготовленного из глины или дерева, и трубки. Открытый конец сосуда покрыт шкурой животного, к которой иногда прикреплена палочка. Двигая палочку вверх-вниз, можно вдувать воздух через фурму глубоко в печь.
После завершения всех приготовлений печь была готова для загрузки. К началу загрузки стенки шахты, вероятно, были очень твердыми. Об этом свидетельствует тот факт, что в кирпичах, из которых выкладывали стенки, не было найдено кусочков древесного угля и руды. При загрузке уголь и руда помещались в шахту, вероятно, чередующимися слоями до полного его заполнения. Поскольку нижняя часть печи не имела больших отверстий, загрузка угля и руды производилась сверху.
Загруженную печь разжигали кусочком тлеющего древесного угля, введенного через фурму в центр печи в ее основании. По мере повышения температуры начинался процесс получения железа. Этот процесс обычно состоит из двух этапов: восстановления железа из окисла и отделения железа от минералов, которые превращаются в шлак. На первом этапе кислород, введенный через фурму, соединяется с углеродом, содержащимся в древесном угле. Двуокись углерода, образующаяся в результате восстановительных реакций, выделяется через шахту в атмосферу. Восстановление железа начинается при температуре примерно 800°С.
Второй этап — отделение шлака — начинается при температуре примерно 1150°С, при которой плавятся посторонние минералы. Температура плавления железа примерно 1540°С. Поскольку само железо не должно было плавиться, температура в печи поддерживалась в пределах 1150—1538°С. В результате процесса восстановления получалась твердая губчатая масса — крица — со шлаковыми включениями. Крицу снова нагревали и ударами молота отделяли шлак. Из полученного железа изготавливали оружие, орудия труда.
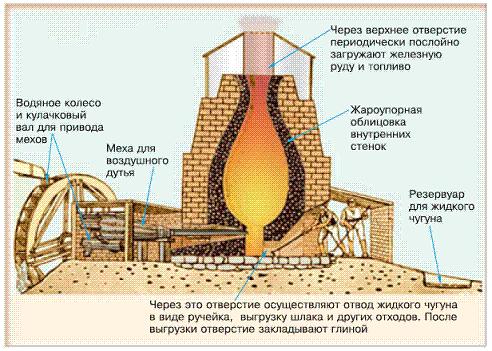
На этом рисунке изображен усовершенствованный вариант печи с отверстием для слива шлаков и металла.
Если принять что вместо железной руды после БП мы будем использовать железный лом, то приведенные печи вполне годятся для плавки железа в «промышленных» масштабах.
Немного раскажу о том что делать с полученной крицей, опять же на примере японских оружейников. После плавки на дне печи остаются слиток чугуна, стали и шлаков (крица) весом до тонны. Рабочие разбирают стены у печи. Затем физическим воздействием дробят слиток приблизительно на дюжину больших кусков. Используя кувалды, рабочие разбивают эти куски необработанной стали на маленькие кусочки размером с кулак для осмотра и сортировки.
Полученные куски после плавки имеет неоднородную структуру со множеством отверстий и частей с различной концентрацией углерода. Блестящий и чистый цвет говорят о том, что это высокоуглеродистая сталь (содержание углерода выше 1 процента). Более темный, грязный цвет указывает на низкое содержание углерода и возможное наличие примесей.
Приблизительно половину составляет сталь, содержание углерода в которой от 0,6 до 1,5 процента. Приблизительно две трети от этой половины составляет сталь оптимального качества с содержанием углерода в пределах 1,0…1,2 процента.
Оставшаяся часть содержит высоко- и низкоуглеродистые куски стали, которые могут быть объединены в процессе ковки. С помощью кузнечной сварки. Не являющаяся сталью половина крицы может быть преобразована в годное для использования сырье за счет увеличения или уменьшения содержания углерода во время специальной процедуры ковки. Углерод, внесенный в сырую железную руду за счет сжигания древесного угля в печи, распределен в крице неравномерно.
Два связанных процессов, которые раньше использовали, чтобы регулировать содержание углерода в таких типах стали и сделать их подходящими для изготовления оружия или инструментов.
Метод, который используемый для обработки малоуглеродистой стали, аналогичен процессу в в высокой печи. Сначала покрывается дно кузнечного горна хорошо измельченным древесным углем. Затем добавляется большие куски угля и зажигаются. После этого укладывается слой малоуглеродистой стали и сверху засыпает еще одним слоем древесного угля. По мере сгорания угля горячая сталь опускается ко дну горна, объединяясь с углеродом, обогащаясь им.
Метод, используемый для высокоуглеродистой стали, несколько отличается и использует способности горячего железа выделять углерод в присутствии кислорода (используется выгорание углерода). Дно горна покрывается золой соломы, смешанной с порошком древесного угля (зола соломы выполняет роль связки и предотвращает распыление порошка напором воздуха из кузнечных мехов). Затем мастер укладывает горкой слой высокоуглеродистой стали так, чтобы в центре горки оставалось свободное пространство и чтобы воздух от кузнечных мехов поступал по воздуховоду непосредственно в центр горки. Сверху все это засыпается слоем древесного угля. После зажигания каменного угля мастер начинает энергично качать мехи, чтобы сохранить устойчивый поток воздуха в раскаленную массу стали. Поступающий кислород объединяется с углеродом, содержащимся в стали и выходит наружу в виде двуокиси углерода. После этого в горне остается металл с уменьшенным содержанием углерода, более пригодный для ковки и сварки.
Но это все о плавке железа и стали в «промышленных» масштабах, а что делать если возникнет необходимость в небольших порциях плавки или в плавке цветных металлов или алюминия.
Тут нам придет на помощь плавка в тигле. Главное правильно подобрать материал тигля и соорудить печь с достаточным поддувом воздуха. Для примера лично плавил ЦАМ (как некоторые говорят алюминий) в консервной банке на костре.
Считайте что плавильная печь для плавления в тигле это тот же кузнечный горн, только закрытый. То есть с термоизоляцией, которая обеспечивает меньший расход топлива (например угля). Для примера приведу чертеж печи(не мой) для плавки небольших порций стали, которая вполне годится для плавки цветных металлов.
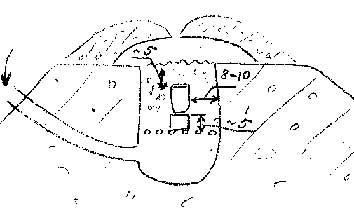
Как видите тигель располагается на камнях или кирпичах, чтобы свободно проходил воздух от мехов, а вокруг тигля насыпан древесный уголь. При хорошем поддуве такая печь разгоняется до температур достаточных для варки стали.
Главный вопрос при тигельной плавке — это сам тигель. Для плавки цветных металлов вполне можно приспособить толстостенную стальную или чугунную посуду (утятница например), идеально вообще подходит обрезанный баллон от маленького огнетушителя.
В случае с железом с тиглем придется помучатся — его, в этом случае, рекомендуют изготавливать из смеси шамотной крошки 50%, шамотной глины 50% и древесных опилок 10% от всего объема. Этой сухой смесью набивают форму для тигля(кувшина) и его предварительно обжигают. Шамотная крошка это битый шамотный кирпич.
Вот написал это и понимаю, что вряд ли после БП будут доступны магазины где продается шамотный кирпич и шамотная глина, поэтому немного отвлекусь про глины. Они бывают разные, в том числе и с различной температурой плавления, шамотная глина самая тугоплавкая — серо-желтоватого цвета. Так что если захотите плавить металлы после БП придется поэкспериментировать с разными глинами — пообжигать горшков и посмотреть как они ведут себя в печи на разных температурах, но это уже ближе к гончарному ремеслу. Просто еще раз обращаю внимание, что при изготовлении должна быть ИМЕННО СМЕСЬ (см. выше).
О литье металла. Часть 2 — собственно литье (совсем немного).
Различают литье в литейные формы и по выплавляемым моделям. Рассматривать различия в литье цветных и черных металлов мы не будим, думаю — умные люди разберетесь.
Литейную форму создают в формовочном ящике, изготавливаемом из неструганых досок (для лучшего контакта с формовочной землей) и называемом опокой. Размеры опоки должны быть примерно в 1,5 раза больше размеров детали. Опока (рис. 1) состоит из двух частей: нижней (ящик с дном) и верхней (рамка с двумя-тремя поперечинами в середине). Для прочного соединения обеих частей опоки на ящике устанавливают фиксаторы, а на рамке делают углубления.
Формовочная земля состоит из 75 % чистого мелкого песка, 20 % глины и 5 % каменноугольной пыли (честно говоря пофиг какого угля). Все компоненты должны быть тщательно перемешаны до получения однородной массы. Для легкоплавких цветных металлов возможно использование гипса, цемента и других строительных смесей для изготовления форм (см. статью о строительных смесях). Поэтому во первых форму из гипса(и других строительных смесей — далее просто гипс) необходимо тщательно сушить, и не в печке, а на открытом воздухе!!! Сушка в печке приводит к снижению прочности гипса и его раскрашиванию и осыпанию. В случае недосушки гипса, при заливке метала, остаточная вода от высокой температуры моментально превращается в пар, это приводит к разрушению формы, образованию полостей (пузырей в отливаемой детали) и что не безопасно, к разбрызгиванию металла!!! Во вторых при высоких температурах гипс начинает терять даже ту воду что он вобрал при отвердении, и как следствии превращается в непрочную, мелоподобную массу поэтому гипс годится только для литья относительно легкоплавкими металлами (олово, свинец).
Возможно изготовление формы для ажурных изделий из чистой глины. Глину для литейной формы нужно хорошо отмутить, то есть удалить из нее посторонние примеси.
Широко известен способ отмучивания глины в воде. Разведенной в воде глине дают отстояться — песок и щебенка опускаются на дно, а травинки и щепки поднимаются на поверхность. Осторожно слив воду, снимают верхний слой глины. Подсушенную глину пускают в дело.
Есть и другой, менее известный способ отмучивания. Куски глины высушивают на солнце или в помещении, а затем толкут в ступе. Растолченную в порошок глину просеивают через мелкое сито, в котором после просеивания остаются посторонние примеси. По мере необходимости глиняный порошок растворяют в воде, получая глину любой консистенции. Из жирной глины можно изготовлять формы для небольших отливок, а из тощей (с добавлением мелкого речного песка) — для крупных. Чтобы глина была однородной, в течение нескольких минут энергично разминайте ее руками.
Теперь об изготовлении формы.
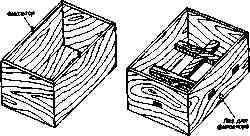
Моделью для изготовления формы может служить как сама деталь, так и специальная модель, выполненная из дерева или иного материала.
При формовке в нижнюю часть опоки насыпают формовочную землю и слегка ее утрамбовывают. Модель припудривают порошкообразным углем или аналогичной сухой пылью и вжимают ее в землю наполовину. Размещают модель таким образом, чтобы выступы и другие ее части легко вынимались из формы и не разрушали ее. Землю в ящике снова посыпают присыпкой, на нижнюю часть опоки устанавливают верхнюю, совмещая фиксаторы с отверстиями. В части будущей детали ставят коническую пробку широкой частью кверху для формирования литника, через который расплавленный металл будут заливать в форму (рис.).
После этого в опоку с избытком насыпают формовочную землю и хорошо ее утрамбовывают. Затем очень аккуратно вынимают пробку под литник, острым предметом снимают верхнюю часть формы и вынимают модель из нижней. На обеих частях формы должны быть углубления, которые точно отображают форму детали. Иногда приходится подправлять модель тонким гибким ножом, удаляя излишки формовочной земли или, наоборот, добавляя ее в том месте формы, где она прилипла к модели и вынулась вместе с ней. Если деталь длинная, то в одном ее конце устраивают литник, а в другом формируют отверстие, аналогичное литниковому, но служащее для удаления воздуха из формы по мере заполнения ее расплавленным металлом. После подсыхания обеих половин формы, их соединяют и хорошо сжимают, чтобы не осталось щели между верхней и нижней частями. В результате получилась форма, готовая к заливке металлом.
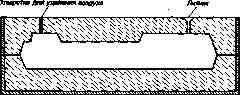
Плавят металл в тигле, имеющем носик (желательно), через который расплавленный металл заливают в литниковое отверстие формы. В качестве печи используют небольшой горн.
После расплавления металл 4—5 мин выдерживают в печи для максимального прогрева. Эта операция способствует качественному заполнению формы в тонких местах. Расплавленный металл заливать в форму необходимо непрерывной, но тонкой струёй, чтобы не происходило размывания формы.
После полного остывания металла форму разнимают и вынимают готовую деталь. Изделия, получаемые описанным методом, как правило, имеют шероховатую поверхность и нуждаются в дополнительной чистовой обработке.
Рассмотрим теперь технологию литья более сложную, чем предыдущая, но позволяющую получать изделия высокого качества и точности. Эта технология дает возможность отливать в условиях БП технические изделия сложной формы вплоть до скульптур, барельефов и прочего.
Модель будущего изделия изготавливают из воска, парафина или иного легкоплавкого материала, затем ее заформовывают в неразъемной жаростойкой массе. При незначительном нагревании или даже кипячении в воде восковую модель выплавляют из формы через отверстие (будущий литник), а в полученную форму заливают расплавленный металл. При тщательном формовании данный способ позволяет повторить в изделии мельчайшие элементы модели. В некоторых случаях выплавлять восковую модель нет смысла — льют прямо туда — воск выгорает.
В сравнительно большие формы расплавленный металл затекает под действием собственного веса, вытесняя находящийся там воздух. Но если отливка имеет маленькие размеры, то хорошего качества изделия добиться невозможно, так как воздух не позволяет жидкому металлу заполнить все полости формы. Преодолеть эту трудность можно, поместив форму в ручную центрифугу (в простейшем случае — ведро с веревкой, сам пользовался). Центробежная сила помогает вытеснить воздух и дает возможность металлу полностью заполнить все пустоты формы. Однако производить эту операцию необходимо быстро, пока металл находится в расплавленном состоянии и крайне осторожно.
Готовую отливку вынимают из формы, разрушая отливку. Затем механическим путем удаляют литник и каналы для отвода воздуха (если они есть). При необходимости готовое изделие подвергают косметической обработке.
В конце несколько слов об еще одном виде литья — шликерном литье.
Выделку керамической посуды мы привыкли связывать с гончарным кругом, а изготовление глиняных фигурок — с обычной лепкой. Но есть и другие способы, и среди них — шликерное литье. Оно дает возможность с большой точностью передавать тончайшие детали, особенно когда нужно изготовить несколько совершенно одинаковых тонкостенных сосудов или небольших керамических деталей.
Шликер — это глина, разведенная водой до состояния, напоминающего густые сливки. Форма, в которую наливают шликер (гипсовая или глиняная — желательно обожженная), вбирает в себя воду. При этом слой глинистой массы равномерно оседает на внутренних поверхностях формы, образуя стенки будущего изделия. Излишек шликера сливается из формы. После высыхания полое глиняное изделие извлекают из формы, досушивают, а потом обжигают. Такова в общих чертах схема шликерного литья.
Для начала приведу технологию плавления чугуна и стали в «высоких» печах которыми пользовались наши предки повсеместно по всему миру.
При сооружении высоких печей сначала выкапывали яму под горн. Насколько большими были такие ямы, сказать сложно, поскольку эрозия почвы и деятельность людей привели к разрушению их верхнего края. Судя по тем горнам, у которых сохранились обожженные края, некоторые ямы имели диаметр около 1,4 м и глубину примерно 75 см. Дно и стенки горна были иногда обработаны; в некоторых случаях обработка состояла в выравнивании их глиняной поверхности.
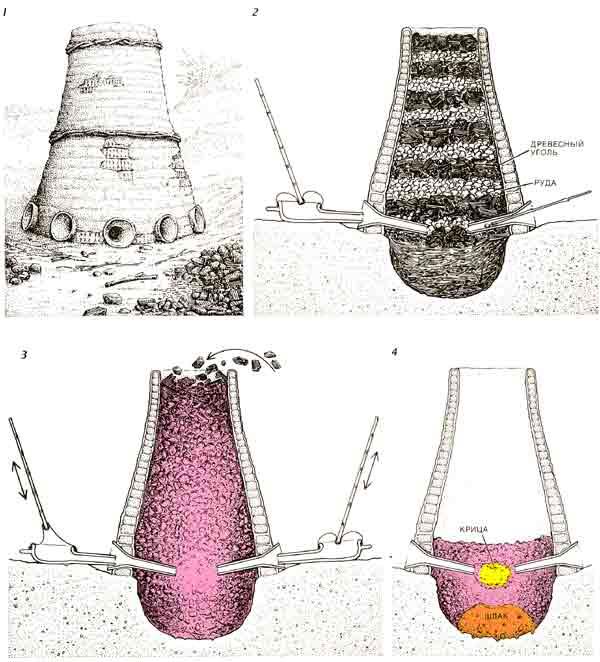
Шахта печи была оштукатурена и скреплена виноградными лозами для придания прочности (7). В основании печи располагались фурмы (трубы для дутья). Шахта загружалась чередующимися слоями древесного угля и руды (2). В открытый конец фурм вставлялись меха, огонь разжигали тлеющим углем, а дополнительное количество древесного угля загружалось сверху (3). Конечным продуктом была крица (4).
ОСНОВНЫМИ элементами, позволявшими использовать дутье, были фурмы. Эти глиняные трубки известны по этнографическим описаниям, а также по археологическим раскопкам. Судя по этнографическим описаниям, все фурмы изготавливали одним способом. Тщательно приготовленную влажную глину налепливали на круглые шесты; после того как глина слегка высыхала, шесты вытягивали, и таким образом получались глиняные трубки. Эти трубки, иногда вставленные одна в другую, вводили в основание печи. Внешнему концу некоторых трубок придавали воронковидную форму, с тем чтобы облегчить вдувание воздуха. Воронковидный конец трубки был обнаружен в стене печи, раскопанной в Гисагаре. Эта находка подтвердила предположение о том, что в печах железного века использовалось дутье.
Вполне вероятно, что в открытый конец фурмы вставляли меха. До сих пор археологами не найдены меха, однако о них часто упоминается в этнографических описаниях, относящихся к Межозерью. Меха, используемые в этом районе и в настоящее время, состоят из крупного сосуда, изготовленного из глины или дерева, и трубки. Открытый конец сосуда покрыт шкурой животного, к которой иногда прикреплена палочка. Двигая палочку вверх-вниз, можно вдувать воздух через фурму глубоко в печь.
После завершения всех приготовлений печь была готова для загрузки. К началу загрузки стенки шахты, вероятно, были очень твердыми. Об этом свидетельствует тот факт, что в кирпичах, из которых выкладывали стенки, не было найдено кусочков древесного угля и руды. При загрузке уголь и руда помещались в шахту, вероятно, чередующимися слоями до полного его заполнения. Поскольку нижняя часть печи не имела больших отверстий, загрузка угля и руды производилась сверху.
Загруженную печь разжигали кусочком тлеющего древесного угля, введенного через фурму в центр печи в ее основании. По мере повышения температуры начинался процесс получения железа. Этот процесс обычно состоит из двух этапов: восстановления железа из окисла и отделения железа от минералов, которые превращаются в шлак. На первом этапе кислород, введенный через фурму, соединяется с углеродом, содержащимся в древесном угле. Двуокись углерода, образующаяся в результате восстановительных реакций, выделяется через шахту в атмосферу. Восстановление железа начинается при температуре примерно 800°С.
Второй этап — отделение шлака — начинается при температуре примерно 1150°С, при которой плавятся посторонние минералы. Температура плавления железа примерно 1540°С. Поскольку само железо не должно было плавиться, температура в печи поддерживалась в пределах 1150—1538°С. В результате процесса восстановления получалась твердая губчатая масса — крица — со шлаковыми включениями. Крицу снова нагревали и ударами молота отделяли шлак. Из полученного железа изготавливали оружие, орудия труда.
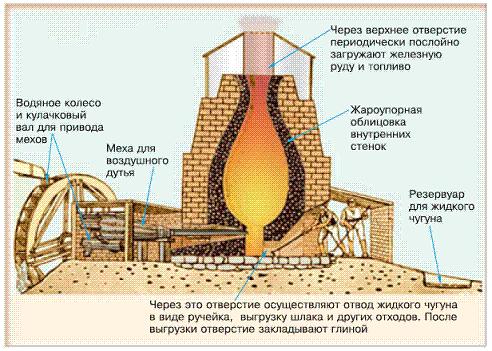
На этом рисунке изображен усовершенствованный вариант печи с отверстием для слива шлаков и металла.
Если принять что вместо железной руды после БП мы будем использовать железный лом, то приведенные печи вполне годятся для плавки железа в «промышленных» масштабах.
Немного раскажу о том что делать с полученной крицей, опять же на примере японских оружейников. После плавки на дне печи остаются слиток чугуна, стали и шлаков (крица) весом до тонны. Рабочие разбирают стены у печи. Затем физическим воздействием дробят слиток приблизительно на дюжину больших кусков. Используя кувалды, рабочие разбивают эти куски необработанной стали на маленькие кусочки размером с кулак для осмотра и сортировки.
Полученные куски после плавки имеет неоднородную структуру со множеством отверстий и частей с различной концентрацией углерода. Блестящий и чистый цвет говорят о том, что это высокоуглеродистая сталь (содержание углерода выше 1 процента). Более темный, грязный цвет указывает на низкое содержание углерода и возможное наличие примесей.
Приблизительно половину составляет сталь, содержание углерода в которой от 0,6 до 1,5 процента. Приблизительно две трети от этой половины составляет сталь оптимального качества с содержанием углерода в пределах 1,0…1,2 процента.
Оставшаяся часть содержит высоко- и низкоуглеродистые куски стали, которые могут быть объединены в процессе ковки. С помощью кузнечной сварки. Не являющаяся сталью половина крицы может быть преобразована в годное для использования сырье за счет увеличения или уменьшения содержания углерода во время специальной процедуры ковки. Углерод, внесенный в сырую железную руду за счет сжигания древесного угля в печи, распределен в крице неравномерно.
Два связанных процессов, которые раньше использовали, чтобы регулировать содержание углерода в таких типах стали и сделать их подходящими для изготовления оружия или инструментов.
Метод, который используемый для обработки малоуглеродистой стали, аналогичен процессу в в высокой печи. Сначала покрывается дно кузнечного горна хорошо измельченным древесным углем. Затем добавляется большие куски угля и зажигаются. После этого укладывается слой малоуглеродистой стали и сверху засыпает еще одним слоем древесного угля. По мере сгорания угля горячая сталь опускается ко дну горна, объединяясь с углеродом, обогащаясь им.
Метод, используемый для высокоуглеродистой стали, несколько отличается и использует способности горячего железа выделять углерод в присутствии кислорода (используется выгорание углерода). Дно горна покрывается золой соломы, смешанной с порошком древесного угля (зола соломы выполняет роль связки и предотвращает распыление порошка напором воздуха из кузнечных мехов). Затем мастер укладывает горкой слой высокоуглеродистой стали так, чтобы в центре горки оставалось свободное пространство и чтобы воздух от кузнечных мехов поступал по воздуховоду непосредственно в центр горки. Сверху все это засыпается слоем древесного угля. После зажигания каменного угля мастер начинает энергично качать мехи, чтобы сохранить устойчивый поток воздуха в раскаленную массу стали. Поступающий кислород объединяется с углеродом, содержащимся в стали и выходит наружу в виде двуокиси углерода. После этого в горне остается металл с уменьшенным содержанием углерода, более пригодный для ковки и сварки.
Но это все о плавке железа и стали в «промышленных» масштабах, а что делать если возникнет необходимость в небольших порциях плавки или в плавке цветных металлов или алюминия.
Тут нам придет на помощь плавка в тигле. Главное правильно подобрать материал тигля и соорудить печь с достаточным поддувом воздуха. Для примера лично плавил ЦАМ (как некоторые говорят алюминий) в консервной банке на костре.
Считайте что плавильная печь для плавления в тигле это тот же кузнечный горн, только закрытый. То есть с термоизоляцией, которая обеспечивает меньший расход топлива (например угля). Для примера приведу чертеж печи(не мой) для плавки небольших порций стали, которая вполне годится для плавки цветных металлов.
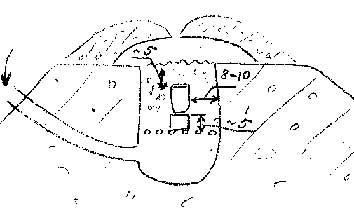
Как видите тигель располагается на камнях или кирпичах, чтобы свободно проходил воздух от мехов, а вокруг тигля насыпан древесный уголь. При хорошем поддуве такая печь разгоняется до температур достаточных для варки стали.
Главный вопрос при тигельной плавке — это сам тигель. Для плавки цветных металлов вполне можно приспособить толстостенную стальную или чугунную посуду (утятница например), идеально вообще подходит обрезанный баллон от маленького огнетушителя.
В случае с железом с тиглем придется помучатся — его, в этом случае, рекомендуют изготавливать из смеси шамотной крошки 50%, шамотной глины 50% и древесных опилок 10% от всего объема. Этой сухой смесью набивают форму для тигля(кувшина) и его предварительно обжигают. Шамотная крошка это битый шамотный кирпич.
Вот написал это и понимаю, что вряд ли после БП будут доступны магазины где продается шамотный кирпич и шамотная глина, поэтому немного отвлекусь про глины. Они бывают разные, в том числе и с различной температурой плавления, шамотная глина самая тугоплавкая — серо-желтоватого цвета. Так что если захотите плавить металлы после БП придется поэкспериментировать с разными глинами — пообжигать горшков и посмотреть как они ведут себя в печи на разных температурах, но это уже ближе к гончарному ремеслу. Просто еще раз обращаю внимание, что при изготовлении должна быть ИМЕННО СМЕСЬ (см. выше).
О литье металла. Часть 2 — собственно литье (совсем немного).
Различают литье в литейные формы и по выплавляемым моделям. Рассматривать различия в литье цветных и черных металлов мы не будим, думаю — умные люди разберетесь.
Литейную форму создают в формовочном ящике, изготавливаемом из неструганых досок (для лучшего контакта с формовочной землей) и называемом опокой. Размеры опоки должны быть примерно в 1,5 раза больше размеров детали. Опока (рис. 1) состоит из двух частей: нижней (ящик с дном) и верхней (рамка с двумя-тремя поперечинами в середине). Для прочного соединения обеих частей опоки на ящике устанавливают фиксаторы, а на рамке делают углубления.
Формовочная земля состоит из 75 % чистого мелкого песка, 20 % глины и 5 % каменноугольной пыли (честно говоря пофиг какого угля). Все компоненты должны быть тщательно перемешаны до получения однородной массы. Для легкоплавких цветных металлов возможно использование гипса, цемента и других строительных смесей для изготовления форм (см. статью о строительных смесях). Поэтому во первых форму из гипса(и других строительных смесей — далее просто гипс) необходимо тщательно сушить, и не в печке, а на открытом воздухе!!! Сушка в печке приводит к снижению прочности гипса и его раскрашиванию и осыпанию. В случае недосушки гипса, при заливке метала, остаточная вода от высокой температуры моментально превращается в пар, это приводит к разрушению формы, образованию полостей (пузырей в отливаемой детали) и что не безопасно, к разбрызгиванию металла!!! Во вторых при высоких температурах гипс начинает терять даже ту воду что он вобрал при отвердении, и как следствии превращается в непрочную, мелоподобную массу поэтому гипс годится только для литья относительно легкоплавкими металлами (олово, свинец).
Возможно изготовление формы для ажурных изделий из чистой глины. Глину для литейной формы нужно хорошо отмутить, то есть удалить из нее посторонние примеси.
Широко известен способ отмучивания глины в воде. Разведенной в воде глине дают отстояться — песок и щебенка опускаются на дно, а травинки и щепки поднимаются на поверхность. Осторожно слив воду, снимают верхний слой глины. Подсушенную глину пускают в дело.
Есть и другой, менее известный способ отмучивания. Куски глины высушивают на солнце или в помещении, а затем толкут в ступе. Растолченную в порошок глину просеивают через мелкое сито, в котором после просеивания остаются посторонние примеси. По мере необходимости глиняный порошок растворяют в воде, получая глину любой консистенции. Из жирной глины можно изготовлять формы для небольших отливок, а из тощей (с добавлением мелкого речного песка) — для крупных. Чтобы глина была однородной, в течение нескольких минут энергично разминайте ее руками.
Теперь об изготовлении формы.
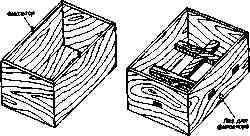
Моделью для изготовления формы может служить как сама деталь, так и специальная модель, выполненная из дерева или иного материала.
При формовке в нижнюю часть опоки насыпают формовочную землю и слегка ее утрамбовывают. Модель припудривают порошкообразным углем или аналогичной сухой пылью и вжимают ее в землю наполовину. Размещают модель таким образом, чтобы выступы и другие ее части легко вынимались из формы и не разрушали ее. Землю в ящике снова посыпают присыпкой, на нижнюю часть опоки устанавливают верхнюю, совмещая фиксаторы с отверстиями. В части будущей детали ставят коническую пробку широкой частью кверху для формирования литника, через который расплавленный металл будут заливать в форму (рис.).
После этого в опоку с избытком насыпают формовочную землю и хорошо ее утрамбовывают. Затем очень аккуратно вынимают пробку под литник, острым предметом снимают верхнюю часть формы и вынимают модель из нижней. На обеих частях формы должны быть углубления, которые точно отображают форму детали. Иногда приходится подправлять модель тонким гибким ножом, удаляя излишки формовочной земли или, наоборот, добавляя ее в том месте формы, где она прилипла к модели и вынулась вместе с ней. Если деталь длинная, то в одном ее конце устраивают литник, а в другом формируют отверстие, аналогичное литниковому, но служащее для удаления воздуха из формы по мере заполнения ее расплавленным металлом. После подсыхания обеих половин формы, их соединяют и хорошо сжимают, чтобы не осталось щели между верхней и нижней частями. В результате получилась форма, готовая к заливке металлом.
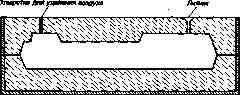
Плавят металл в тигле, имеющем носик (желательно), через который расплавленный металл заливают в литниковое отверстие формы. В качестве печи используют небольшой горн.
После расплавления металл 4—5 мин выдерживают в печи для максимального прогрева. Эта операция способствует качественному заполнению формы в тонких местах. Расплавленный металл заливать в форму необходимо непрерывной, но тонкой струёй, чтобы не происходило размывания формы.
После полного остывания металла форму разнимают и вынимают готовую деталь. Изделия, получаемые описанным методом, как правило, имеют шероховатую поверхность и нуждаются в дополнительной чистовой обработке.
Рассмотрим теперь технологию литья более сложную, чем предыдущая, но позволяющую получать изделия высокого качества и точности. Эта технология дает возможность отливать в условиях БП технические изделия сложной формы вплоть до скульптур, барельефов и прочего.
Модель будущего изделия изготавливают из воска, парафина или иного легкоплавкого материала, затем ее заформовывают в неразъемной жаростойкой массе. При незначительном нагревании или даже кипячении в воде восковую модель выплавляют из формы через отверстие (будущий литник), а в полученную форму заливают расплавленный металл. При тщательном формовании данный способ позволяет повторить в изделии мельчайшие элементы модели. В некоторых случаях выплавлять восковую модель нет смысла — льют прямо туда — воск выгорает.
В сравнительно большие формы расплавленный металл затекает под действием собственного веса, вытесняя находящийся там воздух. Но если отливка имеет маленькие размеры, то хорошего качества изделия добиться невозможно, так как воздух не позволяет жидкому металлу заполнить все полости формы. Преодолеть эту трудность можно, поместив форму в ручную центрифугу (в простейшем случае — ведро с веревкой, сам пользовался). Центробежная сила помогает вытеснить воздух и дает возможность металлу полностью заполнить все пустоты формы. Однако производить эту операцию необходимо быстро, пока металл находится в расплавленном состоянии и крайне осторожно.
Готовую отливку вынимают из формы, разрушая отливку. Затем механическим путем удаляют литник и каналы для отвода воздуха (если они есть). При необходимости готовое изделие подвергают косметической обработке.
В конце несколько слов об еще одном виде литья — шликерном литье.
Выделку керамической посуды мы привыкли связывать с гончарным кругом, а изготовление глиняных фигурок — с обычной лепкой. Но есть и другие способы, и среди них — шликерное литье. Оно дает возможность с большой точностью передавать тончайшие детали, особенно когда нужно изготовить несколько совершенно одинаковых тонкостенных сосудов или небольших керамических деталей.
Шликер — это глина, разведенная водой до состояния, напоминающего густые сливки. Форма, в которую наливают шликер (гипсовая или глиняная — желательно обожженная), вбирает в себя воду. При этом слой глинистой массы равномерно оседает на внутренних поверхностях формы, образуя стенки будущего изделия. Излишек шликера сливается из формы. После высыхания полое глиняное изделие извлекают из формы, досушивают, а потом обжигают. Такова в общих чертах схема шликерного литья.
01 октября 2010, 01:05
+388.46 Nord
— Питер
Про литьё малых форм могу добавить 1) разъёмную форму перед литьём целесообразно закоптить. Например берестой. После этого изделие будит значительно лучше отделяться от формы. 2) для уплотнение и лучшего примыкания к стенкам формы после заливки металла литниковый канал можно заткнуть сырой глиной. Вода из глины закипит, а пар, создавая избыточное давление плотно прижмёт металл к стенкам формы.
З.Ы. А при чём тут шликерное литьё? Мы же о металле говорим…
З.Ы. А при чём тут шликерное литьё? Мы же о металле говорим…
- v
- 0
Комментарии (2)